Deciphering the Enigma of Porosity in Welding: Tips for Minimizing Defects and Taking Full Advantage Of Quality
In the detailed world of welding, porosity continues to be a relentless obstacle that can dramatically influence the quality and honesty of welded joints. As we dive right into the depths of porosity in welding, revealing the secrets to its prevention and control will certainly be vital for professionals looking for to grasp the art of high-grade weldments.
Understanding Porosity in Welding
Porosity in welding, a common concern run into by welders, describes the existence of gas pockets or gaps in the welded material, which can jeopardize the integrity and quality of the weld. These gas pockets are commonly trapped during the welding process due to different aspects such as improper securing gas, polluted base products, or incorrect welding criteria. The development of porosity can weaken the weld, making it susceptible to fracturing and corrosion, inevitably leading to architectural failings.
Recognizing the source of porosity is essential for welders to properly avoid its event. By acknowledging the value of keeping correct gas protecting, guaranteeing the cleanliness of base products, and optimizing welding settings, welders can significantly decrease the possibility of porosity formation. Furthermore, using techniques like preheating the base product, employing correct welding methods, and conducting complete evaluations post-welding can further help in reducing porosity issues. Generally, a detailed understanding of porosity in welding is important for welders to generate top notch and long lasting welds.
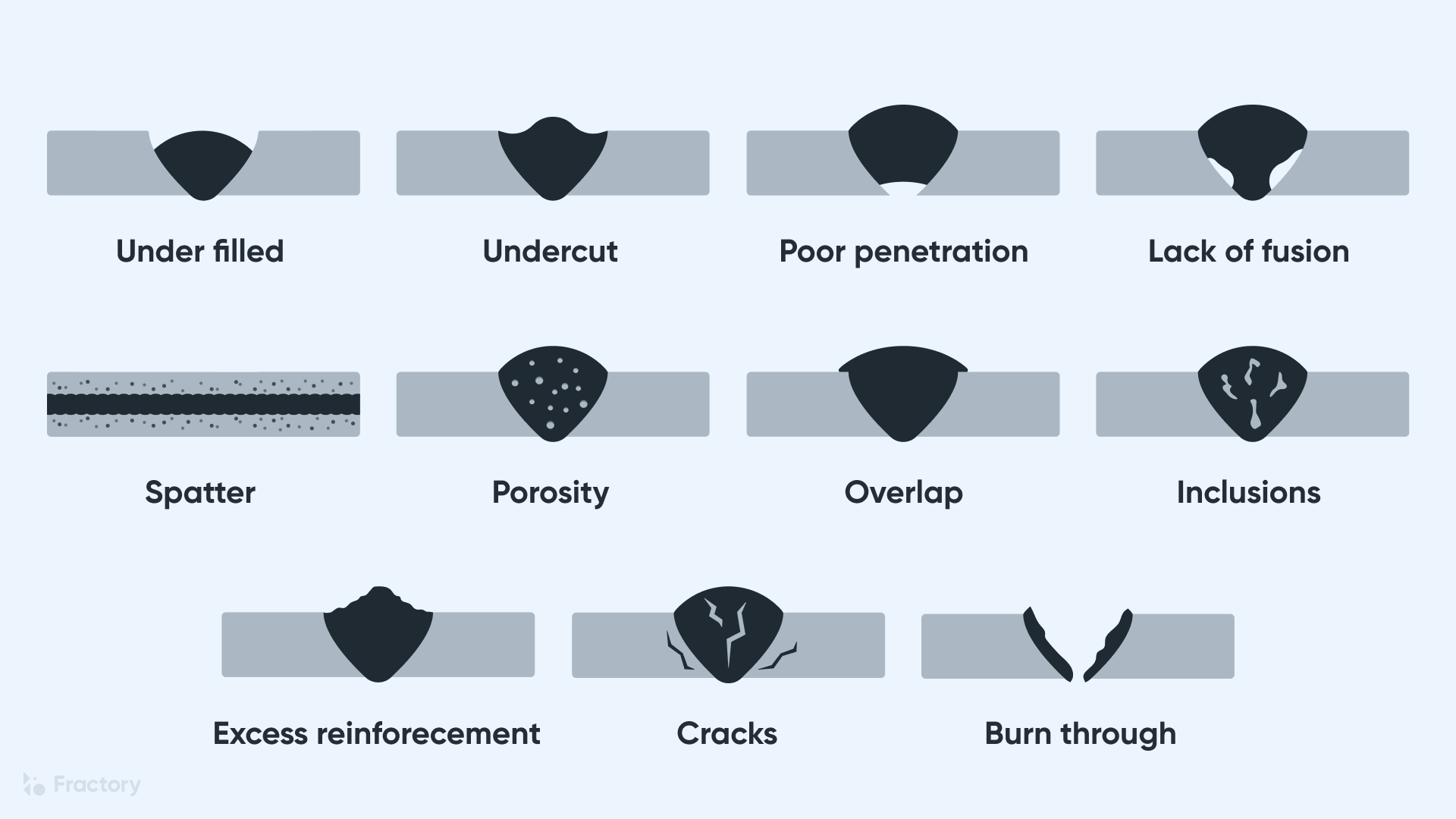
Usual Reasons For Porosity
When inspecting welding processes for possible top quality concerns, understanding the common sources of porosity is necessary for keeping weld integrity and stopping structural failings. Porosity, defined by the visibility of cavities or spaces in the weld steel, can considerably compromise the mechanical residential properties of a bonded joint. One common source of porosity is incorrect securing gas insurance coverage. Poor securing gas flow prices or incorrect gas mixtures can bring about atmospheric contamination, leading to porosity development.
Another prevalent root cause of porosity is the visibility of wetness and impurities on the surface area of the base metal or filler material. When welding products are not effectively cleansed or are subjected to high degrees of humidity, the evaporation of these pollutants throughout welding can create gaps within the weld bead. Additionally, welding at incorrect specifications, such as excessively high traveling rates or currents, can create excessive disturbance in the weld swimming pool, capturing gases and causing porosity. By dealing with these common reasons via correct gas shielding, product prep work, and adherence to ideal welding parameters, welders can lessen porosity and improve the high quality of their welds.
Strategies for Porosity Avoidance
Carrying out reliable precautionary measures is essential in reducing the incident of porosity in welding procedures. One method for porosity avoidance is making sure appropriate cleansing of the base steel prior to welding. Contaminants such as oil, oil, rust, and paint can bring about porosity, so comprehensive cleaning using suitable solvents or mechanical techniques is important.

Using high-quality filler materials and shielding gases that are suitable for the base metal and welding procedure can dramatically reduce the danger of porosity. In addition, maintaining proper welding criteria, such as Continued voltage, present, travel rate, and gas flow rate, is crucial for porosity prevention.
In addition, using appropriate welding techniques, such as keeping a constant travel rate, electrode angle, and arc size, can help stop porosity (What is Porosity). Ample training of welders to guarantee they follow finest practices and quality control procedures is likewise crucial in lessening porosity issues in welding

Finest Practices for Quality Welds
Making certain adherence to industry criteria and proper weld joint preparation are basic facets of achieving continually high-quality welds. In addition to these fundamental actions, there are several ideal practices that welders can carry out to further check my source enhance the quality of their welds. One key technique is keeping correct cleanliness in the welding area. Impurities such as oil, oil, rust, and paint can detrimentally affect the top quality of the weld, leading to issues. Completely cleansing the workpiece and surrounding area prior to welding can help alleviate these concerns.
An additional finest method is to meticulously choose the suitable welding parameters for the particular materials being signed up with. This consists of setting the appropriate voltage, present, travel speed, and securing gas flow rate. Correct criterion selection ensures optimal weld penetration, blend, and general top quality. Using high-grade welding consumables, such as electrodes and filler metals, can significantly affect the final weld top quality. Purchasing costs consumables can result in more powerful, more durable welds with fewer problems. By following these finest techniques, welders can consistently produce top notch welds that fulfill industry criteria and exceed consumer assumptions.
Importance of Porosity Control
Porosity control plays an essential role in ensuring the integrity and high quality of welding joints. Porosity, characterized by the visibility of dental caries or gaps within the weld steel, can substantially compromise the mechanical homes and architectural stability of the weld. Extreme porosity compromises the weld, making it a lot more vulnerable to cracking, corrosion, and total failing under operational tons.
Reliable porosity control is vital for keeping the preferred mechanical residential or commercial properties, such as stamina, ductility, and toughness, of the bonded joint. What is Porosity. By decreasing porosity, welders can boost the general quality and dependability of the weld, guaranteeing that it satisfies the performance demands of the desired application
Moreover, porosity control is crucial for attaining the preferred visual appearance of the weld. Too much porosity not that site just compromises the weld however additionally interferes with its visual appeal, which can be vital in industries where appearances are necessary. Proper porosity control techniques, such as using the correct securing gas, regulating the welding parameters, and ensuring appropriate cleanliness of the base materials, are important for creating high-quality welds with very little issues.
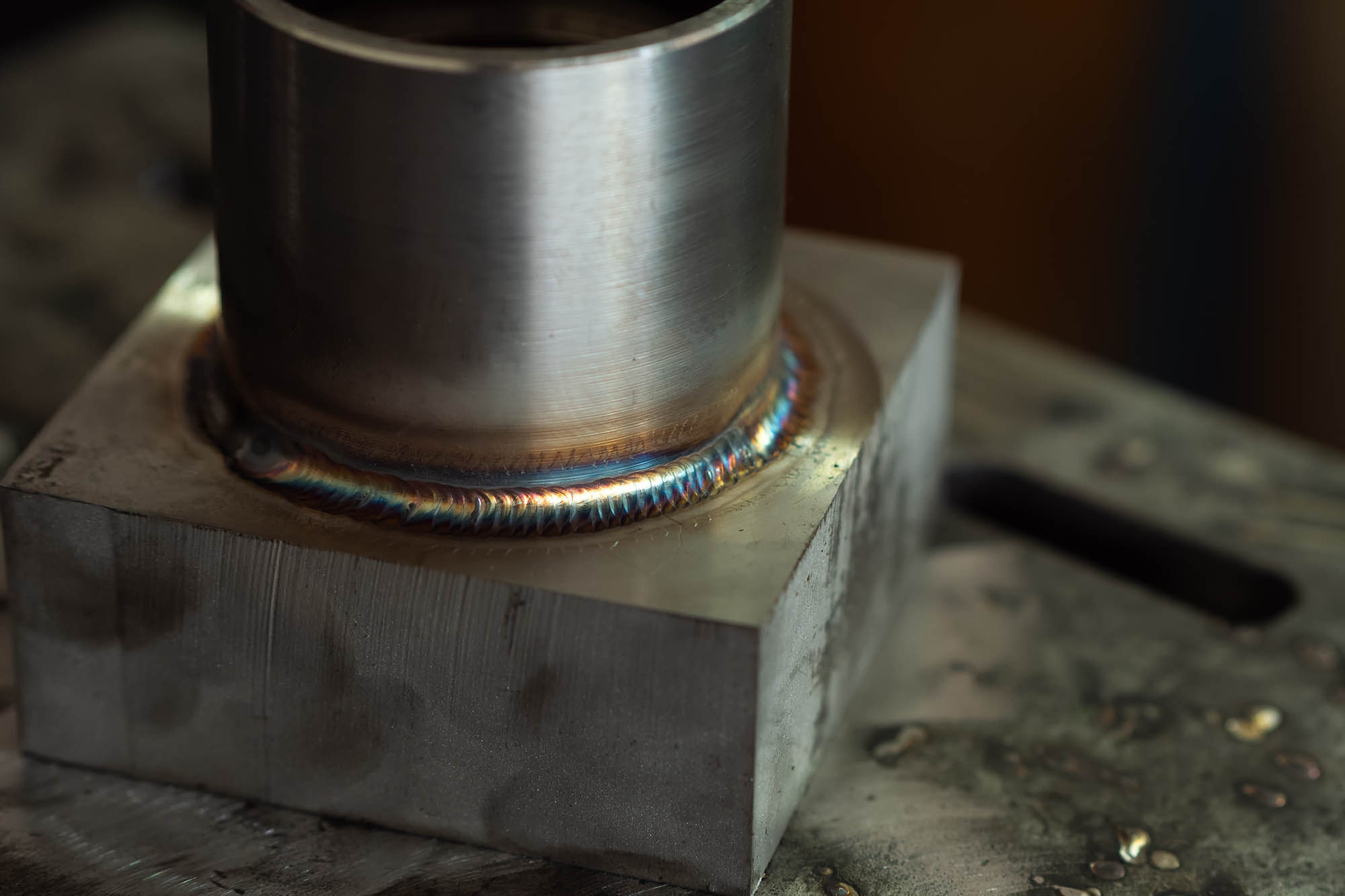
Final Thought
To conclude, porosity in welding is an usual defect that can endanger the high quality of the weld. By comprehending the root causes of porosity and executing appropriate avoidance techniques, welders can lessen defects and achieve better welds. It is vital to regulate porosity in welding to make certain the honesty and stamina of the final item. Executing finest practices for porosity control is essential for accomplishing optimum welding results.